What is flash?
Flash refers to the defect of where excessive material found in the parting position of the mold, especially at the parting surface, movable core, exhaust hole, or exhaust ejector pin.
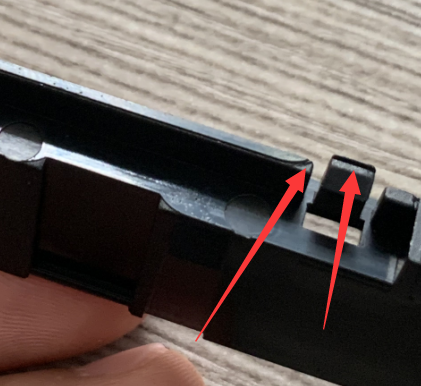
Flash cause reason.
- Low clamping force.
If the clamping force of the injection molding machine is too weak to fix the templates together during the molding process, the flash will occur. - Clearance in the mold.
If the mold structure is deformed, the parting surface is defective, the machine and the mold are improperly set, and there are flying edges or foreign bodies glued to the parting surface, the flying edge will occur if the parting surface can not be completely contacted. - Molding conditions.
Inappropriate molding conditions, such as high melt temperature (thinning the melt) or high injection pressure, can lead to flash. - Improper venting.
A poorly designed ventilation system, a very poor ventilation system, or a ventilation system that is too deep can lead to flash.
Remedies:
- Adjust mold settings.
Set up the mold to seal correctly. A mismatch or unwanted gap between the mold cavity and the core side will result in a flash.
Make sure the template is strong enough to avoid deformation during the forming process.
In the molding process, if the template is deformed, you can increase the pillar support or thicken the template.
Check that the ventilation size is adequate.
The recommended ventilation size for crystalline polymers is 0.025 mm (0.001 in.), for amorphous polymers is 0.038 mm (0.0015 in.).
Clean the mold surface.
Due to the residual foreign body between the parting surfaces, the poor sealing of the mold surface may lead to flying edges.
Grind off the surface to keep the sealing pressure in the area around the cavity high enough.
2. Adjust machine settings.
Set up the machine and mold to seal correctly. The poor sealing between the mold cavity and the core side, as well as the non-parallelism of the machine table, may lead to flash.
Increase the size of the injection molding machine. Insufficient clamping force of the machine will lead to flash.
If the machine capacity is sufficient for the clamping force, adjust the clamping force.
- Adjust the forming conditions.
Reduce the cylinder temperature and nozzle temperature.
High melt temperature will reduce the melt viscosity and make the melt thinner, resulting in flash evaporation. However, it should be noted that the melt temperature is too low, resulting in the required high injection pressure leading to flash.
Reduce injection pressure and packing pressure to reduce clamping force requirements.
Reduce the feed setting (stroke length) to reduce metering (overfilling).
Increase the injection time or slow down the injection speed.