Believe it or not, plastic injection molding is very old. The first injection mold machine was made by two brothers in the 19th century. With advancements in technology, we have made the art of injection molding better. We now have small machines that can fit on our tabletops.
Plastic injection involves placing molten plastic material in a mold cavity. The process of injecting needs high pressure to make parts and prototypes. The high pressure forces the molten material to all corners of the mold cavity. These molds may be made of hardened steel or aluminum. The disadvantage of plastic injection molding is the time required to make molds.
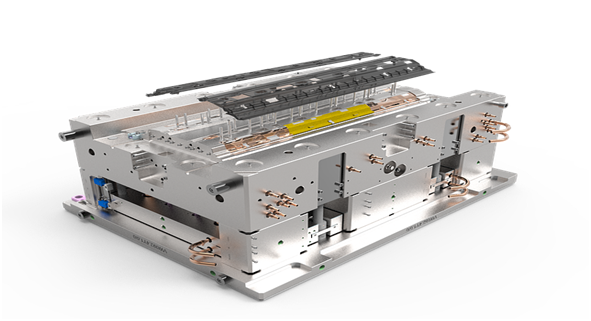
On some occasions, you may need CNC machines to remove support structures. You can use a mold for a long time without changing the dimensions of the mold. The initial cost of a mold may be high, but the mold’s output covers this. Once you have a mold, you can replicate parts or prototypes several times. This will see to it that your production process is cost-efficient.
So, what are some of the advantages of plastic injection molding?
Automation
Plastic injection molding is done by machines. You do not need a lot of workers to run the process. This way, you can reduce the cost of production since you do not need human labor. Machines can work all over the clock without fatigue. Injection molding is ideal for producing mass parts of the same dimensions. We do not know what the future holds. One thing we are all waiting for is the integration of AI and IoT. If this were to happen, we would marvel at the power of automation, imagine what we could do with such power. The plastic industry has a fast-paced market. Meaning that manufacturers must shorten their production processes to ensure a constant supply. With automation, you can reduce the time required to produce parts and prototypes. This is because the process is continuous and can run for hours. With little human intervention, comes the added benefit of reduced errors.
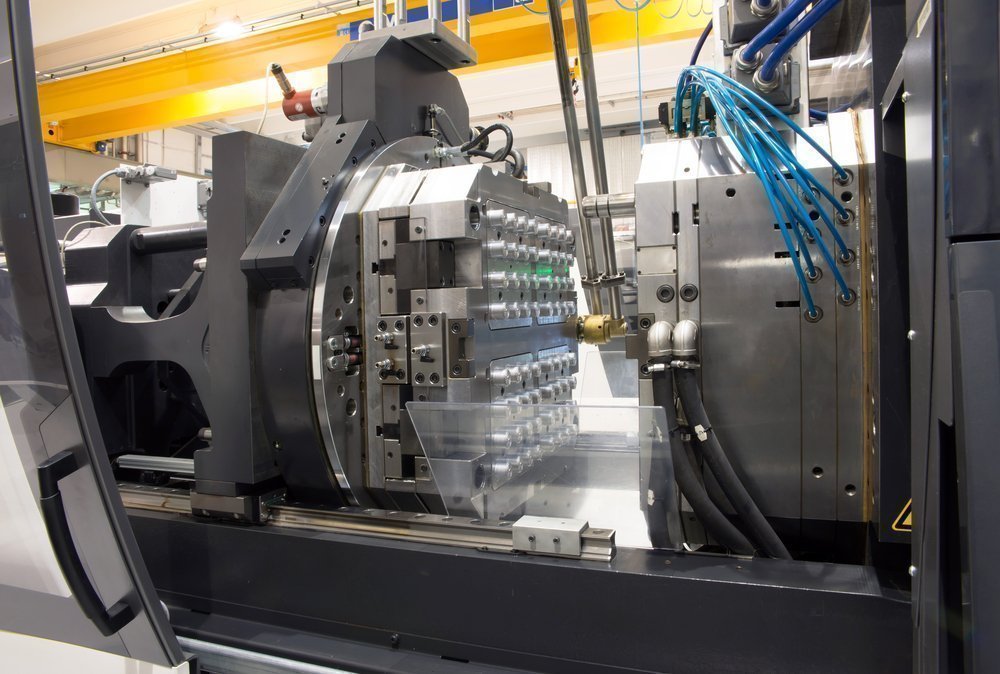
Efficient
Plastic injection molding is quite efficient once you have a mold. Making parts with plastic injection molding is quite fast. This is because most plastics cool fast. Aluminum molds also draw heat away from the parts. These factors allow machines to work fast. If you have a steel or an aluminum mold, you can make several parts with the same mold. This way, you will be saving on some expenses. Optimizing your production process will see to it that you deliver quality services. Customer satisfaction in the plastic industry is paramount. To increase your profit margins and grow, you need to reduce the cost of production.
Wide range of materials
Plastic injection molding gives you the chance to pick from a wide variety of materials. Plastics usually have a lower melting point making them ideal for the process. The molten plastic material is injected into the mold cavity. You can opt to add dye or coloring to your part as required. Some of the materials are; Acrylonitrile butadiene styrene (ABS), Polycarbonate, Nylon, Polypropylene, Polyethene.
Compared to metals, plastic have the following advantages;
· May have higher tensile strength than some metals.
· Low melting point
· Lower product weight
Precision
Molds allow you to work with complex geometries and small parts with low tolerances. The heated material is injected into the mold cavity at high pressures. Thus, dimensional accuracy is not an issue. Surface finishing under injection mold is like no other. Where support structures are required, you can remove them by simple machining. Other post-production processes like sanding and polishing. Take look at aluminum for part and prototype production. You will notice that the products need post-production processes. These processes are mostly for surface finishing like anodizing aluminum. All these are extra costs, which could lower your profit margins. Plastic injection allows you to create high precision parts. Not to mention quality surface finishing at a lower price.
Increased strength
With plastic injection molding, you can enhance strength by adding fillers. These fillers go along with the material during the injection. Some industries need parts that can face extreme conditions without caving in. Injection molding with fillers will go a long way in making your parts strong and durable.
Design flexibility
In case you are thinking about making changes in the design of your mold, the task is easier than you think. Making iteration on the cavity mold is relatively cheap and easy to apply. You can also add engravings in the mold to suit your brand or needs.
Low Volume Injection Molding and 3D printing
A steel or aluminum mold usually takes around two weeks to a month to make. This is unacceptable in the plastic market since it is a fast-paced market. Manufacturers are forced to adapt to the market’s state. Most of them are going into low volume injection. You are wondering what low volume injection is, right?
Low volume injection involves the use of lesser durable molds that take up lesser time to create. The mold is built for short runs and cannot make many parts compared to hardened steel or aluminum molds. The goal here is to reduce the time required to produce plastic parts with injection molding. One of the best ways to create short term mold is the use of a 3D printer. A 3D printer can create a mold in a matter of hours. Not only will you be reducing the time required to make a mold, but also the cost.
Here are some of the advantages of low volume injection molding
Shorter lead time. Under plastic injection, the most time-consuming stage is mold creation. With a 3D printer making short-term molds, you can produce molds fast and in quick succession. So, even if a mold reaches the most uses, you won’t take ages to get a new one. If you are producing parts, you will have more time to assess the market. Then you can plan on how to position yourself to ensure that you sell out.
Cost-saving. If you were to compare the cost of a pre-hardened steel mold and a lower grade mold, you would notice a disparity. Molds made for low volume injection have lower grade aluminum. Lower-grade aluminum is readily available and relatively cheap. Lower-grade aluminum is not the only material used in making molds.
Bridging tool. Low volume injection produces a notch higher than prototyping. But, it produces quantities lower than full production. Manufacturers use low volume injection as a bridging tool before starting full production. Bridging is a vital stage in the production processes. You are producing low volumes while testing the market. While at it, you can easily make changes to your design. You do not want to have large amounts of parts without a marketing strategy.
Inventory management. Common mistake manufacturers make is committing to full production. While at it, the cost of storage and inventory management becomes too high. In the end, you will find yourself getting rid of some parts. You still need space to store new parts. Working with low volumes gives you the ease of management. This way, you will reduce the risk of damage or misplacement.
The role of 3D printing in plastic injection molding
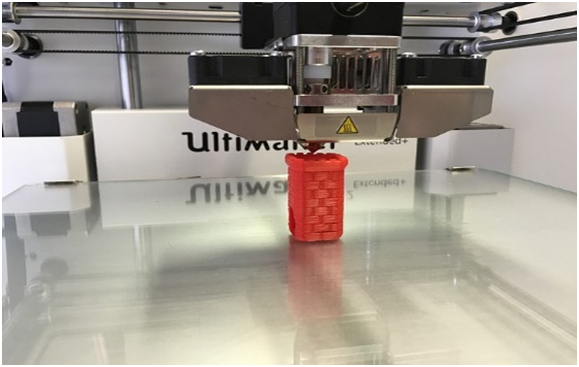
Stereolithography (SLA) 3D printing is one of the best and most effective ways to make molds. The molds produced are stable and isotropic. It means that they can work with the high pressures of injection molding. 3D printed molds have design flexibility allowing manufacturers to make iterations. You can make changes fast meaning that you still maintain the short lead time needed.
Compared to CNC machining, 3D printing is the best choice. This is because it involves additive manufacturing, unlike machining. This implies that you do not have to worry about waste. No to say that CNC machining is obsolete in the process. Some parts produced through injection molding need CNC machining. Machining is used to shave off excess material and support structures. Machining molds may take up a lot of time, not to mention the costs involved. With an affordable 3D printer, you can make molds with less time and at a lower price. Of course, the investment capital for a functional 3D printer may be daunting. But the output outshines the expenses incurred. Remember that all you need is a CAD file, and within a few hours, your mold is ready.
Prototype Injection Molding
Manufacturing without prototyping is like building a house without blueprints. When you decided you do not have time to prototype, then you are planning to fail. Prototyping is not actual production, meaning that you should not spend a lot of time on it. But, we should give credit where it is due. The processes of prototyping need speed. You want your prototypes to reach the market for customer feedback and modifications. Non-functional prototypes are best made of plastic. Injection molding is vital at this juncture.
Advantages of prototype injection molding:
Efficient. Durable steel and aluminum molds can serve you for a long time. Molds made through machining do not have sharp corners on the inside but have a radius. Sometimes this may inconvenience you. Removing corners in parts or molds increases strength.
Part made through injection molding may have higher tensile strength. You can by adding fillers. You can also add coloring in the material while injecting it into the cavity.
Affordability. Prototype injection molding is affordable if you factor out the cost of making molds. Even with the high price of mold creation, the rest of the process requires little capital to run. Automation further makes the cost of plastic injection cheaper.
When is prototype injection molding appropriate?
· When you cannot machine the material. Some plastics are flexible, making it hard for CNC cutters and millers to work on them.
· When you need high precision, tight tolerance, and complex geometries. Small parts with complex geometries are best made through injection molding.
In a nutshell, manufacturers have different methods of production at their disposal. These methods are; CNC machining, Injection molding, 3D printing, and Casting. Each process has advantages and disadvantages. How you manipulate them to work for you will determine your success. One drawback of injection molding is the loss of structural integrity. Heating the material causes the final products to lose structural integrity. Shorter lead time means that you will have time to test the market. It is also an excellent bridging tool from prototyping to full production.